
Aşağıdaki Teknik Bilgiler Kısa Adı MEGEP Olan; T.C Milli Eğitim Bakanlığı Mesleki Eğitim ve Öğretim
Sistemini Güçlendirme Projesinin Resmi Web Sitesinden Derlenmiştir. | | 6- Flexo Baskı Kontrolü | | | | 12- | | | 13- | | | 14- | | | 15- |
| |
1. BASKI TAŞIYICININ MAKİNADAN GEÇİŞİNİ KONTROL ETMEK
1.1. Baskı Malzemeleri
Flekso baskı tekniği ile esnek, esnek olmayan malzemeler, çok küçük ebatlı işlerden, büyük ebatlı işlere kadar her türlü malzemeye baskı yapılabilir. Düşük viskoziteli flekso baskı mürekkepleri ve bu mürekkeplerin yüksek tutunma özellikleri bu baskı sistemine geniş bir ürün yelpazesine baskı yapma olanağı tanımaktadır.
1.2. Baskı Yolunun Tanımı
Flekso baskıda baskı yapılacak malzemenin çözgü ünitesine bağlanıp sargı ünitesine kadar geçen yola baskı yolu denir. Çözgüde açılan bir baskı malzemesi ilk başta avare merdane olarak adlandırılan merdaneler arasından geçirilerek makinenin fren sistemine gelecek olan yük azaltılmış olur. İş baskı kazanına gelir. Baskı yapıldıktan sonra yine avare merdane diye nitelendirdiğimiz merdaneler arasından geçerek, baskı taşıyıcı fırındaki merdaneler arasından sargı ünitesine gelir. Basılan ürün burada sarılarak kesime hazır hale gelir. Flekso baskıda bu yola baskı yolu denir.
1.3. Kenar Kontrol Ayarları
Flekso baskıda basılan bobinin baskı esnasında gezinmesini önleyen fotoselli ayara kenar kontrol ayarı denir. Gerek baskıya giren gerekse baskıdan çıkan ürünün düzgün bir şekilde sarılmasını sağlar.
1.4. Çözgü ve Sargı Kontrolleri
Baskıya
giren mal ile baskıdan çıkan malın ağırlıkları ve bobinlerin dönme
sayıları birbirinden farklıdır. Aynı zamanda baskıya giren malın
çözülmesi için harcanacak kuvvet ile baskıdan çıkan malın sarılacağı
bobine harcanacak kuvvet te tamamen birbirinden farklıdır. Bu
değişkenleri kontrol altında tutan sisteme fren sistemi denir.
Basılacak ürün esnek bir ürün ise çözgü ve sargı senkronizasyonu daha
fazla önem kazanmaktadır. Çözgü ve sargı kontrolünü yapan fren sistemi
yardımıyla bu işlem kontrol altına alınır.
1.5. Sensör Kontrolleri
Baskı
esnasında flekso baskı makinelerinde basılan işin kontrolünü gözle
yapmak mümkün değildir. Makineyi durdurup kontrolleri yapmak da hem iş
gücüne hem de zaman kaybına sebep olur. Örnek verecek olursak dakikada
200 metre hızla baskı yapan bir makinede basılan işin kontrolü özel bir
sistem aracılığıyla yapılır. Bu sistemin çalışması bir fotoğraf
makinesinin çalışma sistemine benzer. Profesyonel bir fotoğraf
makinesinde hızla giden bir arabanın fotoğrafını çekmek için anlık
ayarını 500’e getirip o arabanın fotoğrafını çekebiliyorsak ve o
arabanın durmuş vaziyetteki fotoğrafını görebiliyorsak, sensör kontrolü dediğimiz
olay da makinenin baskı esnasındaki hızına orantılı olarak enstantanesi
artan ve azalan bir fotoğraf makinesi yardımıyla görüntü bilgisayara
aktarılır. Bu görüntüye bakılarak yapılan baskının tam oturup
oturmadığı kontrol edilir. Bu bilgiler ışığında baskı ayarları tekrar
yapılır.
1.6. Fırın Sıcaklık Kontrolü
Flekso
baskıda kullanılan mürekkeplerin içinde solventler bulunmaktadır.
Bundan dolayı solventlerin buharlaştırılması da hava dolaşımı ile
olduğundan Flekso baskıda fırın sıcaklığı kurumayı etkileyen en önemli
etmendir. Flekso baskıda fırın sıcaklık kontrolü ortamın ısısına göre
değişir. Kış aylarında 50-60 °C iken yaz aylarında bu sıcaklık 30-40 °C
kadar düşürülür. Fırın sıcaklığı fazla olursa basılan ürün deforme
olur. Eğer fırın sıcaklığı normalinden az olursa yapılan baskı
kurumadan sargıya sarılır. Bundan dolayı baskıdaki renkler de
bozulmalar ve yayılmalar meydana gelir.
1.7. Düz ve Ters Baskı Yönü Kontrolü
Flekso
baskıda düz ve ters baskı yönünün kontrolü, grafik aşamasındayken
yapılması gerekir. Ters baskı yönü genelde gıda malzemelerinde ve
şeffaf malzemelere uygulanır. Şeffaf malzemeye baskı yapılırken, filmde
görüntü ters, kalıpta görüntü düz, baskıda görüntü ters olur. Düz
baskıda ise filmde görüntü düz, kalıpta ters baskıda düzdür.Düz ve ters
baskı da renk sıralaması da farklılık gösterir. Örnek verecek olursak
düz baskıdaki renk sıralaması ve ters bakıdaki renk sıralaması
aşağıdaki tabloda olduğu gibi olur.
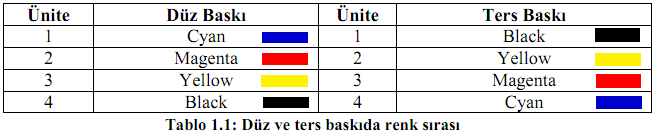
1.8. Baskı Renklerini Kontrol Etmek Baskı renklerinin kontrolü basılacak işin kenarlarına konulan kroslar yardımıyla veya baskı kenarına konan renk kontrol noktaları yardımıyla yapılır. Flekso baskıda baskı esnasında kontrolleri yapmak güç olduğundan dolayı renk kontrolü yine kamera (Sensor) aracılığıyla yapılır. Bu renk değerleri yine kamera yardımıyla ekrana aktarılıp ekranda değerlere göre renk şiddeti artırılır veya noktanın nokta üzerine oturtulması için gerekli ayarlar yapılır. Renk kontrolünde nokta ayarı aşağıdaki şekilde gösterilmiştir.
1.9. Renk Yapışmasını Kontrol Etmek
Renk
yapışmasının kontrolü basit yöntemlerle yapılır. Baskısı yapılan bir
ürün üzerindeki mürekkebin baskı malzemesine yapışıp yapışmadığı bir
selotyp yardımıyla yapılır. Eğer selotyp kaldırıldığında renkte yolma
meydana gelmediyse mürekkep uygun şekilde yapışmıştır eğer mürekkepte
yolunma var ise baskı malzemesi yüzeyinde veya kullanılan mürekkebin
yapısında bozulmalar var demektir. Çözüm olarak kullanılan
mürekkep değiştirilir, kullanılan malzeme değiştirilir veya yüzeyi
korona işlemi gerekiyorsa korona işlemi uygulanır. Diğer bir renk
kontrol yöntemi ise orijinal ile basılan numunenin
renklerikarşılaştırılarak göz ile kontrol edilir.
1.10. Matbaada Kalite Kontrol
Günümüz
rekabet koşullarında müşteri memnuniyetini sağlamak gün geçtikçe daha
da zorlaşıyor. Bu yüzden artık ürünlerinizin ve sunduğunuz hizmetlerin
kalitesini izlemek ve geliştirmek zorundasınız. Üretimde kullanacağınız
malzemelerin, işletmenize girdikleri andan itibaren kendilerinden
beklenen özellikleri taşıyıp taşımadıkları belirlemeli ve bu
malzemelerin üretimin farklı aşamalarında gerek kendi özelliklerinden
gerek üretim prosesinden kaynaklanan hatalarını izlemelisiniz. Ancak bu
şekilde nihai ürününüzün müşteri beklentilerine uygun halde
üretilmesini sağlayabilirsiniz.
2. BASKI VE KURUMANIN KONTROL EDİLMESİ 2.1. Baskı Görüntü Ayarları Baskıda görüntünün net çıkabilmesi makine üzerinde birçok ayara ve kullanılan baskı malzemesine göre değişir. Bunlar genel olarak şu ayarlara bağlıdır.
- Renk oturtma (Krosları oturtma) - Viskozitenin görüntüye etkisi - Baskı kaymasının kontrol edilmesi - Forsa (Basınç) etkisi 2.2. Renk Oturtma
Flekso baskı renkleri oturtulurken krosların tam oturması gerekir aksi takdirde bobine basıldığından dolayı baskı renkleri oturmaz. Özellikle trigromi baskıda bu daha da önem kazanır. Flekso baskıda baskı silindirleri ileriye geriye doğru hareket ettirilerek renkler tam olarak üst üste oturtulur. Silindire montajda kalıbın çarpık olmaması gerekir. Herhangi bir kalıbın silindire montajında çarpık şekilde oturtulursa renkler üst süte oturmayacaktır. Böyle bir durumda yeni kalıp çekilerek tekrar silindire montajı yapılmalıdır.
2.3. Viskozitenin Görüntüye Etkisi
Flekso
baskıda, mürekkebin viskozitesinin baskıya etkisi diğer baskı
tekniklerinde olduğu gibi flekso baskıda da önemlidir. Viskozitesi
düşük olduğunda mürekkep içerisindeki solvent miktarı fazladır. Buda
baskıda renklerin açılmasına baskıda tram hat keskinliğinin
kaybolmasını sağlar. Eğer mürekkebin viskozitesi yüksek olursa, baskıda
yolmalar meydana gelir. Görüntü netliğinin kaybolmasına ve baskının
koyulaşmasına neden olur.
2.4. Baskı Kaymasının Kontrol Edilmesi
Baskıda
kaymanın kontrol edilebilmesi, makine üzerinde daha baskıya başlamadan
yapılan ayarların doğru ve düzgün yapıldığından emin olmamız gerekir.
Baskıya girecek baskı altı malzemesinin baskı esnasında çözgü ve sargı
ayarlarının tam ve doğru yapılması gerekir doğru yapılmayan çözgü ve
sargı ayarı basılan bobinin gevşekliğinden dolayı tramlar da kaymalar
olur. Aynı şekilde bobin baskı esnasındayken aşırı gergin halde baskı
yapılırsa yine baskıda kaymalar oluşur.
2.5. Forsa (Basınç) Etkisi
Flekso
baskıda forsa basıncının az veya çok olması her iki durumda da baskıda
problem oluşturur. Forsanın yüksek olması baskıda tramların, yazıların
veya çizgilerin şişmesine neden olur. Flekso baskıda naylonprint klişe
kullanıldığından basınçtan dolayı tramlar daha çabuk büyüdüğünden forsa
ayarının daha hassas yapılması gerekir.
2.6. Kurutma Üniteleri
Flekso
baskıda kurutma üniteleri genelde iki şekilde yapılır. Bunlar sıcak
hava üfleme yoluyla yapılan kurutmalar ikincisi ise basılan işe direkt
sıcak hava vererek yapılan kurutma yöntemidir. Her iki yöntemde de amaç
mürekkep içerisinde bulunan solventlerin atılmasıdır.
2.6.1. Kurutma Ünitelerinin Yapısı
Kurutma
ünitelerinde hava baskıdayken basılan işin üzerine üflemek suretiyle
mürekkebin kuruması sağlanır. Bu yöntemle çalışan makinelerde hava
üflemesi yapılan yerdeki hava delikleri dar açılı V şeklindedir. Bunun
nedeni üflenen havanın karşı tarafa çarpıp geri gelmesiyle hava
dağılımını eşit yapmaktır. Diğer bir yöntem ise ısınan rezistanslar
aracılığıyla baskıdan çıkan malzemenin bu sıcak ortamdan geçirilerek
üzerinde bulunan solventlerin atılmasıdır. Yandakii resimde baskı
ünitesinden çıkan baskı malzemesi üzerine sıcak hava üfleyen kurutma
ünitesinin resminde de görüldüğü gibi dışarıda ısınan hava hortumlar
aracılığıyla baskıya üflenmektedir. | 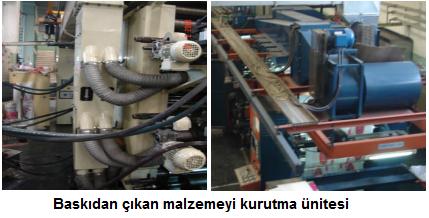 | 2.6.2. Kurutma Ünitelerinin Sıcaklığını Sabitleme
Kurutma ünitesinin sıcaklığı sabit bir sıcaklığa ayarlanarak basılan malzemenin kuruması sağlanır. Bu sıcaklık sabitlemesi de makinenin teknik yapıdan gelişmişliğine bağlıdır. Teknolojik açıdan gelişmiş makinelerde makinenin sıcaklığı belli bir derecede sabitlenir. 2.6.3. El İle Kuruma Kontrolü Yapmak
El ile kuruma kontrolü yapmak flekso baskıda tercih edilmeyen bir yöntemdir. Özellikle makine sürekli baskıya geçtiğinde, elle kontrol yapmak imkansızdır. Makine baskıya hazırlık aşamasında ise, basılan baskı altı malzemesine elimizi hafif sürttüğümüzde eğer mürekkep elimize bulaşmıyor ise renklerde dağılma bozulma meydana gelmiyor ise baskımız yeterince kurumuş demektir. Eğer bulaşma ve renklerde bozulma var ise ya mürekkebin viskozitesi düşük veya mürekkep içerisinde bulunan alkol tiner vb. gibi incelticilerin miktarı azaltılmalıdır. 3. RAKLE VE BASKI ÇIKIŞININ KONTROL EDİLMESİ3.1. Raklenin TanımıFlekso baskıda boyanın dengeli bir şekilde baskıya verilmesi için kullanılan metal aparata rakle denir. Raklenin amacı haznesinin içinde dönen merdane üzerinde fazla olan mürekkebi alarak baskıda ihtiyaç olan kadar merdane gözeneklerinde kalan mürekkebi kalıba transfer etmektir. Rakle aparatı içinde kalan mürekkep haznedeki mürekkeple sürekli desteklenerek hem homojen mürekkep sürekli transferi sağlanır hem de kurumanın önüne geçilmiş olunur. 3.2. Rakle Problemleri Flekso
baskıda kullanılan rakle problemleri genelde raklenin uzun süre
kullanımından meydana gelen aşınmalarından kaynaklanmaktadır. Raklenin
taşıyıcı merdane üzerinde aşırı forsa ayarından mürekkebin az gitmesi
ve dolayısıyla görüntüde netlik oluşmaz. Rakle basıncı az olduğu
takdirde de fazla mürekkepten dolayı görüntü detayları kaybolur. Ayrıca
raklenin etrafından hiçbir şekilde mürekkep sızması meydana
gelmemelidir. Mürekkep sızmasının oluşması baskıda renk
farklılaşmasının yanında tramlı işlerde tramların dolmasına sebep olur.
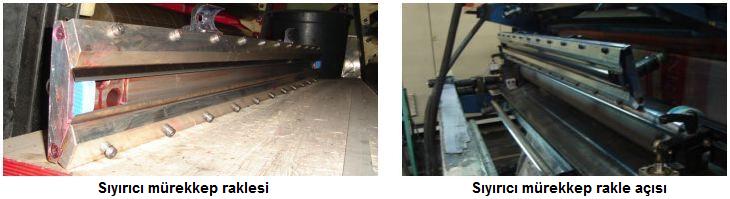
3.4. Rakle Açıları
Flekso
baskıda kullanılan raklelerin açıları yatay ile 60-70°’dir. Dikey ile
20-30°’dir.Rakle açıları genelde sabittir. Raklenin forsa ayarı ile çok
azda olsa açısı değişir. Fakat raklenin forsa ayarı fazla
arttırıldığında merdanede ve rakleler de aşınma meydana gelir.
Merdanenin de raklenin de ömrü kısalır.
3.5. Kombine Flekso Baskı Makineleri
Flekso
baskı makineleri genelde baskı ünitesi ile baskı sonrası yapılan
işlemler ayrı makinelerle yapılır. Fakat sürekli aynı sektöre üretim
yapan firmalar baskı ünitesi çıkışına kesim kırım tıraş makinesi gibi
üniteler ilave ederek kombine flekso baskı makinesi haline
dönüştürmüşlerdir. Kombine flekso baskı makinelerinde avantajlarının
yanında dezavantajları da mevcuttur. Kesimde çıkan bir problemle
makinenin tamamının durdurulması ve ayar yapılması gerekir. Aynı
şekilde baskıda çıkan bir problemde kesimde devre dışı kalır. Bu
olumsuzluklara rağmen kombine flekso baskı makineleri sürekli aynı işi
basan matbaalarda büyük avantajlar sunmaktadır.
3.6. Baskı Çıkışı Bobin Kontrolü Yapmak
Flekso
baskıda baskı çıkışı bobinin düzgün sarılması için manyetik frenli
tansiyon sistemi kullanılır. Bu sistem sayesinde sargı bölümünde
bulunan malzeme hem sıkı sarılır hem de basınçlı merdaneyle sargıdaki
baskının arasında hava boşluğu kalması önlenmiş olunur. Ayrıca baskı
çıkışında bobinin sargıya gelmeden önce sensör yardımıyla bobinin
gezmesinin önüne geçilerek daha düzgün sarılmasını sağlar.
3.7. Baskı Çıkışı Dilme ve Tıraş Kontrolü Yapmak
Flekso
baskıda baskı çıkışı baskıda fazla olan yerlerin tıraşlanması ve
kesilmesi gereken yerlerin kontrolü makine baskıya girmeden istenen
şekilde ayarlanır. Baskı esnasında pek ayar değiştirilmez. Baskı
esnasında çıkan herhangi bir problemde, makine durdurularak ayar
yapılır. Örnek verecek olursak poşet basan makinede baskı çıkışında
tıraşlama ve kesim makinesinde poşetler ellilik halde kesimi yapılır.
Poşetlerde ağız kısmı yani elle tutulacak kısım ellilik desteler
halinde tıraşlanır.
3.8. Laminasyon İki
veya daha fazla malzemenin birbiriyle yapıştırılması işlemine
laminasyon adı verilir. Laminasyonun amacı; ambalajın içine konulan
gıda maddelerinin bozulmasına neden olabilecek nem, ışık, gaz
geçirgenliklerinin azaltarak istenen korumasını sağlamaktır. Flekso
baskıda laminasyon işlemi genelde gıda maddeleri ambalajına yönelik
işlerde kullanılır. Gıda maddeleriyle temas eden ambalaj gıda
maddeleriyle reaksiyona girer. Buda ambalajlanan maddenin bozulmasına
neden olur. Böyle bir durumda gıda ambalajları çok dikkatli
seçilmelidir.
Eğer seçilen ambalaj gıda ile reaksiyona girecek
bir ambalaj ise reaksiyona girmeyen bir ambalaj içine
yapıştırılmalıdır. Gıda ambalajlarında bazen iki bazen üç ürün aynı
anda lamine edilir. Örnek verecek olursak cips gibi maddeler lamine
edilmeyen ambalajlara konmaz mutlaka gıdanın konacağı ambalaj lamine
edilmelidir.
Flexographic Machine - Flexoprinting - Flexo Baskı Makineleri - Flexo Baskı - Flekso Baskı Makinası
|
Copyright © MATESAN
Makine Teknolojileri
Sanayi - Innovation in the Machinery [ 2010 - 2011 ] info@matesan.com Tel :+90 216 527 35 61 - Fax :+90 216 527 35 62 |